SPECIALTY AIR FILTERS |
||||||||||||||||||||||||||||||||||
(contract last updated 02/03/2023) | ||||||||||||||||||||||||||||||||||
SCOPE: This contract is designed to offer users a variety of manufacturers and distributors from which they can purchase specialized Air Filters and related accessories. The Manufacturers identified are now or have been used on University of Wisconsin campuses for related applications. Users of the contract should note that some of the items listed may be available under mandatory State of Wisconsin-Department of Administration (DOA) contracts. State of Wisconsin Agency and Campus Customers will be required to review products offered through this contract to insure that the products being purchased are not available under the mandatory DOA contract(s). | ||||||||||||||||||||||||||||||||||
CONTRACT # | DESCRIPTION | |||||||||||||||||||||||||||||||||
21-5029 | SPECIALTY AIR FILTERS | |||||||||||||||||||||||||||||||||
CONTRACT ORIGIN: | ADDITIONAL INFORMATION: | |||||||||||||||||||||||||||||||||
UW-Madison Purchasing Services 21 N Park St, 5th Floor Madison, WI 53715-1218 |
UW-Madison users contact: |
|||||||||||||||||||||||||||||||||
Non-UW-Madison users contact: Vendor Representative | ||||||||||||||||||||||||||||||||||
COOPERATIVE PURCHASING: | YES | |||||||||||||||||||||||||||||||||
CONTRACT TERM: | November 1, 2020 through October 31, 2024, with automatic renewal extensions to October 31, 2026, unless amended, cancelled or rebid. | |||||||||||||||||||||||||||||||||
Manufacturer(s) | FILTRATION GROUP and D-MARK | |||||||||||||||||||||||||||||||||
Vendor(s) |
|
|||||||||||||||||||||||||||||||||
Commodity Code | 031-44 | |||||||||||||||||||||||||||||||||
Federal Employee ID # (FEIN) | 39-1533037 | |||||||||||||||||||||||||||||||||
F.O.B. | “D” F.O.B. DESTINATION |
|||||||||||||||||||||||||||||||||
Terms: | N/30 | |||||||||||||||||||||||||||||||||
Delivery: | 14 Days ARO | |||||||||||||||||||||||||||||||||
Warranty: | 1 Year | |||||||||||||||||||||||||||||||||
Invoicing: | Invoices shall reflect contract pricing. | |||||||||||||||||||||||||||||||||
Return Policy: | Contractor will provide for return of items ordered in error for up to 30 calendar days from receipt with the University paying only the return shipping costs. | |||||||||||||||||||||||||||||||||
Back Orders: | Will notify ordering department within 2 working days of order/release. | |||||||||||||||||||||||||||||||||
Pricing Information: | Click here for pricing. | |||||||||||||||||||||||||||||||||
Revision History: |
||||||||||||||||||||||||||||||||||
(3/10/22): updated to show price changes for Filtration Concepts Inc, effective March 9, 2022. | ||||||||||||||||||||||||||||||||||
(2/3/23): updated to show pricing changes for Filtration Concepts Inc, effective immediately. |
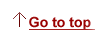